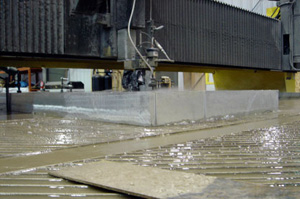
Water jet cutting services enable a wider range of companies to benefit from quick, cost-efficient industrial cutting that does not employ the use of heat. As heat is used as the main cutting source in the majority of different industrial cutting methods, some materials cannot be cut in this manner, as they will suffer from thermal stress. Materials, such as plastic, rubber and glass can melt, distort or warp from industrial cutting methods that use heat.
Water jet cutting is capable of rendering high precision cuts to a wide range of materials, enabling many industries to depend upon this efficient means of cutting. Consider the range of durability and consistency in the following materials:
-
Stainless Steel
-
Aluminum
-
Stone
-
Marble
-
Granite
-
Brass
-
Glass
-
Titanium
-
Rubber
-
Plastic
-
Carpet
The wide range of materials that can be cut by water jet cutting exemplifies the range of industries that have come to depend upon water jet cutting as a means of creating high precision cuts in a variety of unique shapes and patterns.
Why Water?
While the name suggests that water is the main cutting force in this method of industrial cutting, it merely acts as a carrier for an abrasive substance that is responsible for actually slicing through the material at hand.
The abrasive substance, usually sand or garnet, is mixed with the water and pushed through a concentrated area (a nozzle orifice comprised of ruby, diamond or sapphire) with compressed air at a high velocity of 40,000 to 55000 psi or three times the speed of sound. As such, water jet cutting is capable of cutting many materials of large thickness levels (up to .012”) without employing the use of heat.
There are many advantages to selecting water jet cutting over any other industrial cutting method available. The stream is flexible and the multi-axis enables it to render fine lines and shapes, and can even create three-dimensional forms and patterns.
A design is computer generated and then applied with precision by a robotic arm. The kerf width allows for tight nesting and the accuracy points of water jet cutting are up +/- o.oo1. h. Because water jet cutting does not depend on heat, less material ends up wasted on account of melting. Cuts from water jet cutting are smooth, with no burring.
Water jet cutting is used for projects such as the following:
-
Tube cutting
-
Pipe Cutting
-
Net Size Cutting
-
High Precision Cuts
-
Screen Cutting
-
Shape Cutting
More industries are using water jet cutting as a means of reducing their green footprint as well. As the abrasive substance used in water jet cutting is non-toxic, the solution can be used more than once. There is no hazardous waste to dispose of, meaning that water jet cutting does not result in materials that will just remain in landfills for years to come.
Industries are relying more and more on water jet cutting as a cost-efficient and time-effective means of industrial cutting.